Factory in Rzhev
Production processes
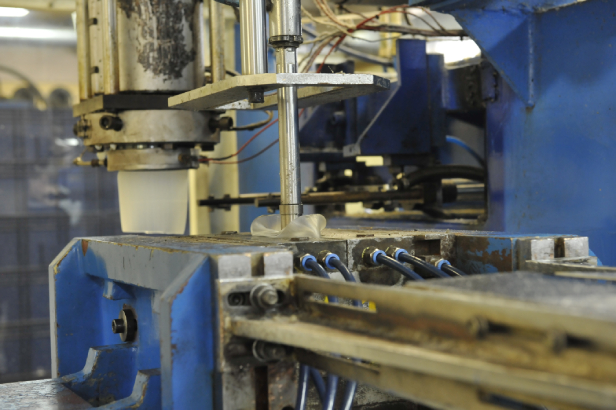
Plastic injection molding is carried out on 7 modern casting machines of one of the industry leaders - HAITIAN with an injection volume of 66 to 270 cubic centimeters and a clamping force of up to 1200 kg from various types of polymers: polyamide, grodnomide, polyethylene, ABC and others. At the plastic injection moulding section, the SMED quick changeover system has been introduced, which allows you to regulate the actions of personnel and reduce downtime.
In addition to casting machines, there is a blow molding machine, with the help of which washer tanks are made. The workers of the workshop are leaders in providing Kaizen with proposals that allow you to combat all types of losses in production.
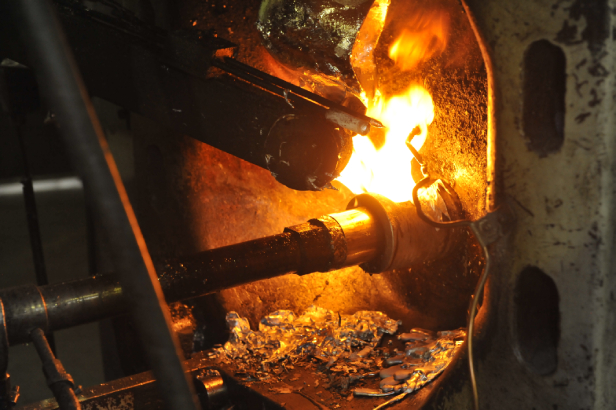
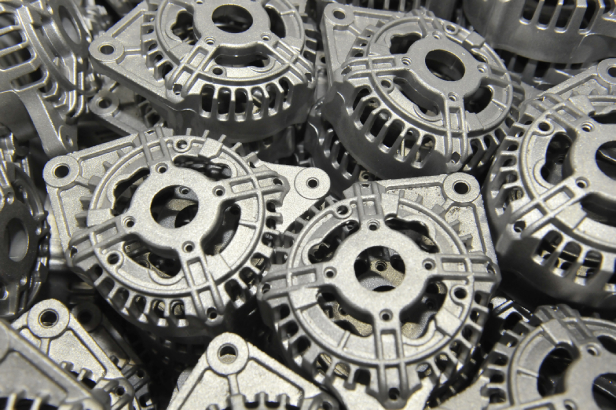
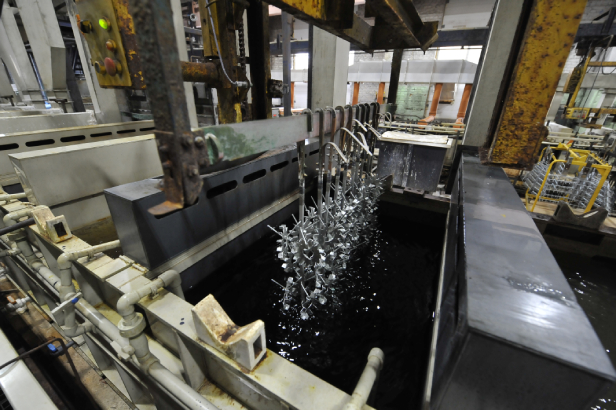
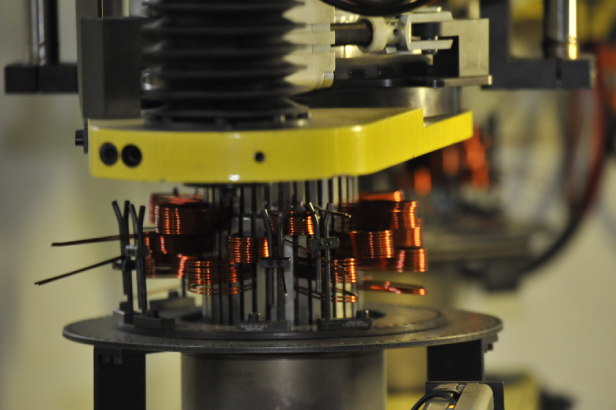
New Product Development Processes
The tasks of the Chief Technologist Department (GBS) include technological preparation for the production of both new products and modernization of existing ones. This process implies a comprehensive systematic approach, which includes the selection of progressive, modern technological equipment necessary for the purchase, the conclusion of contracts for its supply, the monitoring of all stages of its implementation, the organization and direct participation in the commissioning and acceptance of equipment, and the transfer of the streamlined process to the existing production. Also, in the course of production preparation, the design of technological tooling is carried out (both in-house and with the involvement of third-party organizations). In parallel with the development of technological processes, a whole set of documents is developed that meet international quality standards, which is necessary for the presentation of finished products to the Consumer and is a prerequisite for the possibility of starting serial deliveries after obtaining approval from him. This work is carried out on the basis of the requirements of international engineering methods.
The Chief Technologist's Department carries out the design of tooling, such as molds, dies, working and control devices, and means of admission control. The work is carried out using modern, domestic software, including 3D modeling. GBS specialists constantly monitor compliance with technological discipline in production units, timely adjustment of technological documentation aimed at continuous improvement of processes.